Unknown Facts About Alcast Company
Unknown Facts About Alcast Company
Blog Article
An Unbiased View of Alcast Company
Table of ContentsThe Alcast Company DiariesHow Alcast Company can Save You Time, Stress, and Money.Indicators on Alcast Company You Should KnowThe 25-Second Trick For Alcast CompanyHow Alcast Company can Save You Time, Stress, and Money.Alcast Company Things To Know Before You BuyThe Ultimate Guide To Alcast CompanyEverything about Alcast Company
It possessed good toughness and machinability. There are lots of various other aluminum alloys that can be used for casting components. To figure out which alloys would certainly be great for your jobs, contact Impro.
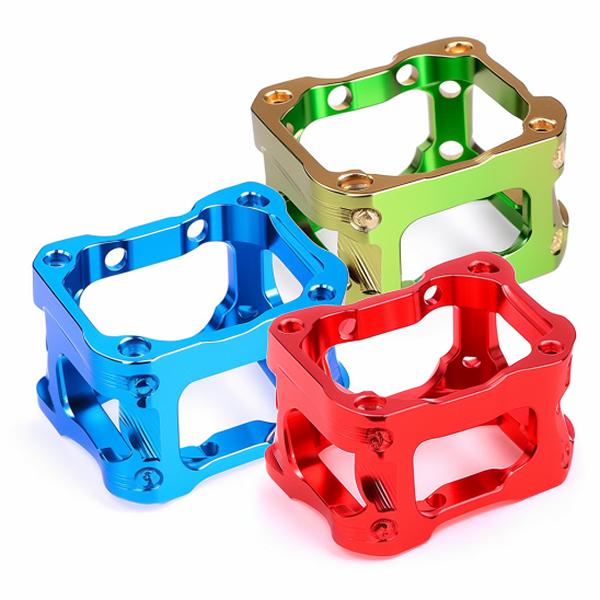
(AA), based in North America, has actually developed specifications that control light weight aluminum alloys' composition, residential properties, and nomenclature. There are two types of light weight aluminum alloys functioned and cast.
What Does Alcast Company Mean?
Cast aluminum alloys are made by melting pure aluminum and combining it with other metals while in fluid form. The mix is poured right into a sand, die, or financial investment mold. After solidification, the steel is eliminated from its mold and mildew. At this stage, it is in either its final kind or as a billet or ingot for more handling.
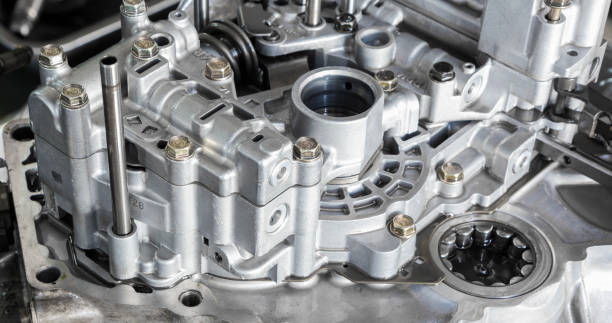
There are many minor differences in between functioned and cast light weight aluminum alloys, such as that cast alloys can consist of much more considerable amounts of various other metals than functioned alloys. The most remarkable distinction between these alloys is the manufacture process with which they will go to provide the final product. Apart from some surface therapies, cast alloys will certainly leave their mold and mildew in almost the exact strong kind preferred, whereas functioned alloys will certainly undergo numerous adjustments while in their solid state
Alcast Company Things To Know Before You Buy
If you think that a wrought alloy may be the very best for your project, have a look at a few of our posts that explain even more concerning certain functioned alloys, such as Alloy 6061 and Alloy 6063. On the various other hand, if you think a cast alloy would be much better for you, you can discover extra regarding some actors alloys in our Alloy 380 and Alloy 383 write-ups (coming soon).
When selecting an aluminum factory for your manufacturing needs, it's critical to examine a number of elements. One of the most critical aspects to take into consideration is the experience and capability of the factory. Choosing a foundry who has the appropriate knowledge of the aluminum spreading procedure, and the portfolio to reveal for it, helps to have a successful end result for your task.
The Facts About Alcast Company Revealed
Having the experience and market expertise to craft your spreadings for ideal production and quality outcomes will improve the project. Producing aluminum spreading needs a complicated set of processes to attain the best outcomes. When selecting a new aluminum factory to companion with, guarantee they have considerable sector experience and are educated concerning all elements of the aluminum casting procedure: layout, manufacturing, material analysis, and item screening.
The factory ought to also have a tried and tested performance history of providing exceptional items that satisfy or exceed consumer assumptions. Quality control should likewise be at the top of your list when picking a light weight aluminum factory. By dealing with a certified foundry that complies with the requirements for quality control, you can protect the honesty of your item and ensure it satisfies your requirements.
Facts About Alcast Company Uncovered
By choosing a business that supplies solutions that meet or exceed your product requirements, you can be certain that your project will be completed with miraculous accuracy and effectiveness. Particular aluminum foundries specialize in particular kinds of producing procedures or casting approaches. Various components call for different production methods to cast aluminum, such as sand casting or die casting.
Pass away casting is the name offered to the process of developing complicated steel elements via use of mold and mildews of the component, additionally known as passes away. It creates even more components than any kind of other procedure, with a high degree of precision and repeatability. There are three sub-processes that drop under the category of die spreading: gravity pass away casting (or long-term mold and mildew casting), low-pressure die spreading and high-pressure die spreading.
The Ultimate Guide To Alcast Company
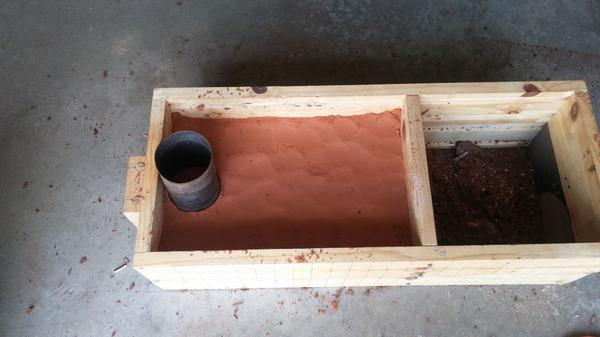
The pure metal, additionally referred to as ingot, is included in the furnace and maintained the molten temperature of the steel, which is then transferred to the injection chamber and infused right into the die. The stress is after that maintained as the metal strengthens. As soon as the metal solidifies, the cooling process starts.
The thicker the wall surface of the component, the longer the cooling time because of the amount of interior steel that additionally requires to cool. After the component is fully cooled, the die halves open and an ejection system presses the part out. Following the ejection, the die is closed for the next injection cycle.
The 10-Minute Rule for Alcast Company
The flash is the additional product that is cast throughout the procedure. This must be trimmed off making use of a trim tool to leave just the primary part. Deburring eliminates the smaller sized pieces, called burrs, after the trimming process. Finally, the part is brightened, or burnished, to provide it a smooth surface.
This confirmed to be an unreliable test, because the tester can cut right into an item and miss a location with porosity - aluminum casting manufacturer. Today, top suppliers utilize x-ray screening to see the entire interior of elements without cutting right into them. This enables them to more properly accept or reject elements. To get to the ended up item, there are 3 primary alloys utilized as die spreading material to pick from: zinc, check that aluminum and magnesium.
Zinc is one of the most used alloys for die casting due to its reduced price of raw products. Its corrosion resistance likewise allows the parts to be lengthy lasting, and it is one of the much more castable alloys due to its lower melting factor.
The 25-Second Trick For Alcast Company
As stated, this alloy is just one of one of the most commonly used, yet manufactures will, at times, select aluminum over zinc due to light weight aluminum's production benefits. Light weight aluminum is highly cost-effective and one of the extra versatile alloys. Light weight aluminum is used for a number of various items and sectors anything from home window structures to aerospace products.
Report this page